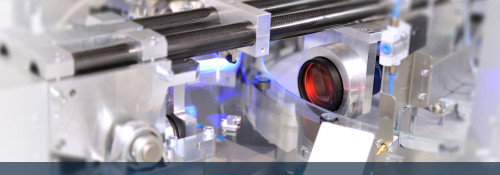
Goods and components are visually inspected using image processing in automatic optical measuring, inspection and sorting machines.
As increasing demands are placed on the quality of parts in many industrial sectors, the automation of quality assurance is essential. Conventional visual inspection in production with the human eye quickly reaches its limits due to the required throughput rates. High cycle rates and the demand for a reproducible, objective 100% inspection are fuelling the demand for automated systems for visual inspection - i.e. automatic visual inspection. In addition, the documentation of quality is becoming increasingly important, as is the integration of all production processes (Industry 4.0).
Automated optical quality control has become an integral part of many production processes. Automated inspection systems for visual inspection are essential, especially for large production batches that need to be inspected quickly and reliably for surface defects and/or dimensional accuracy. The advantages of this type of optical inspection are obvious:
An optical inspection system usually consists of a camera/optics, lighting and image processing software for analysing the images. There may also be mechanical components for positioning the test specimens in front of the optics. Depending on the application, the visual inspection systems can be integrated into existing production lines or used as an individual system to inspect and sort parts in a fully automated process. Coupled with the appropriate feeding and packaging units, this results in inspection and sorting systems for surface inspection that are precisely tailored to the respective requirements.
Optical sorting is based on image acquisition, which forms the basis for evaluation by special software. The quality of the image or, more precisely, the achievement of the best possible contrast is decisive for the quality of the entire inspection. A defect can only be analysed by the software if it can be made visible. Therefore, the components of the image acquisition, i.e. camera, lens and lighting, must always be perfectly matched to the properties of the test objects. Optimised lighting plays a major role, and several options are often tried out in order to achieve the best contrast. For example, diffuse or directional lighting, bright field or dark field arrangements, or incident or backlight illumination can be selected.
As the classification of the test specimens must be carried out virtually in real time, i.e. in a fully automated process, both the hardware components and the image analysis software are of particular importance. The more powerful the hardware and algorithms are, the more complex inspection tasks and higher throughputs the AOI system can realise.
A recurring issue in optical surface inspection and measurement is the so-called pseudo waste. This refers to inspected parts that have been categorised as defective by the inspection system's algorithm, even though they are not actually defective.
There are many reasons for this, e.g. changes to the material, the production process or the environmental conditions that require recalibration of the test system or adaptation of the test programmes. The sensor units used in NELA's testing and measuring systems and our VisionCheck evaluation software, which is continuously developed in-house, offer a wide range of adaptation options to reduce or avoid pseudo waste.
NELA's product programme for automatic inspection covers a wide range of inspection requirements. Our systems are equally suitable for optical surface inspections and for measuring. NELA inspection stations are available in different versions, e.g. as a glass disc system, belt system or intermittent system. Depending on the application, shape & size or material properties of your series parts, we can offer you the right inspection system.
Glass table inspection systems are suitable for fully automatic and non-destructive dimensional accuracy testing, defect inspection and sorting of series parts for various applications. They are used as optical sorting systems, particularly for high inspection requirements, as the glass discs ensure high stability of the entire inspection process, especially during geometry inspection.
Belt-based inspection systems are particularly suitable for inspecting very small parts or parts with an unstable position that cannot be inspected on a glass plate due to an unfavourable height/width ratio. Belt systems are also ideal for parts that are primarily to be inspected for surface defects. The parts can also be flipped over for a complete, all-round inspection.
Indexed systems are workpiece circulation systems that position the test parts individually in front of one or more sensors. These systems are designed for complex parts or very high inspection requirements; both geometric and surface defects can be detected. Elastic parts, such as seals made of rubber or rubber compounds, can be stretched or squeezed to detect hidden defects.
In industries such as the automotive industry and medical technology, for example, there are often very high demands on the quality of technical components, often coupled with a zero-defect requirement. NELA's AOI systems are so universally designed that they are suitable for the visual inspection of a wide variety of series parts used in different industries. Whether turned and milled parts, fasteners or plastic and rubber components, NELA inspection stations are used for a wide range of inspection tasks.
Which visual inspection system is suitable for your industry or application depends on individual factors such as material properties, shape and size, as well as the inspection requirements. Our sales team and our application department will be happy to advise you and, if necessary, prepare a feasibility study.
Even if processes such as CNC milling, turning, etc. are considered safe and precise, quality fluctuations can occur due to malfunctions, variations in the raw material or handling. With an inspection and sorting system from NELA integrated into your production, you can be sure that all parts classified as "good" by the system fulfil the highest quality requirements: Your standards.
Precision and micro-precision turned parts can vary greatly in shape, size and surface finish simply due to different turning processes. Complex geometries and tight tolerances in terms of dimensional accuracy pose particular challenges for quality inspection. NELA's automatic optical inspection systems are set up according to the application in terms of material, surface, shape, size and defect catalogue and equipped with the appropriate feeding, sorting, camera and lighting components.
In addition to dimensional inspection and height testing, the test specimens are also checked for reliable functional performance, e.g. for defect-free surfaces on functional and sealing surfaces.
In the optical inspection of fasteners and formed parts, comprehensive visual surface inspection, including thread inspection, is a challenging inspection task. With our inside and outside sensors specially designed for these applications, we are able to inspect every single micrometre of the component surface, including the thread, for defects. In addition, a high-precision dimensional accuracy check is carried out and the inspected parts can be sorted according to customer-specific configurable criteria. NELA inspection and sorting systems are suitable for a wide range of cold and hot formed parts, fasteners (including rivets, nuts, screws and fasteners), bushes, sleeves and washers!
The high-precision inspection of key contour features and a dimensional accuracy check of your sintered parts is crucial for achieving a high level of customer satisfaction and loyalty. Our high-precision solutions in standardised inspection systems, but also for inspection machines individually tailored to customer requirements, ensure that the frequently reworked outer surfaces of sintered parts are checked for topological damage (edge chipping, efflorescence, cracks and blowholes) and detect abrasive residues.
The precise inspection of the dimensional accuracy and geometry of your punched and fineblanked parts, taking into account the cutting burr height and the punch feed, is crucial for achieving your quality specifications. NELA's automated measuring, inspection and sorting solutions ensure a comprehensive geometry check of your parts. Our inspection systems guarantee a precise dimensional accuracy check and reliable flatness inspection of your sheet metal products.
To ensure maximum customer satisfaction, manufacturers of high-quality plastic or rubber parts, such as seals, must be absolutely certain that all supplied parts fulfil the quality specifications - without deviation. NELA inspection and sorting systems use high throughput, non-contact optical inspection to ensure that every part leaves your production line on time and in perfect condition. Complete surface inspection and dimensional accuracy testing in the micrometre range ensure that even the highest industry standards are met. By squeezing and/or stretching elastic parts, even hidden defects such as cracks can be detected.
Hydrogen will play a major role in the development of renewable energies in the future, whereby the storage of hydrogen as an energy source and its conversion into electrical energy will be of particular importance. The bipolar plates used in hydrogen technology fulfil important functions within the fuel cells, as they
Bipolar plates are therefore an integral component of hydrogen fuel cells, but they are susceptible to damage and defects during the manufacturing and processing process, which can affect the effect of the plates, e.g. as a seal or conductor. It is therefore essential to detect these defects and damage as early as possible, including deformation, oxidation, foreign particles and air bubbles.
NELA measuring and testing systems can check the properties that are important for the function of the plates and detect the corresponding defects. As bipolar plates are highly reflective, which poses a challenge for defect inspection, shape-from-shading technology is used. Corresponding sensors are integrated into the inspection stations and incorporated into the software.
NELA is a member of the BW Fuel Cell Cluster, which is driving the further development of hydrogen technology towards serial production. Further information: https://www.e-mobilbw.de/netzwerke/cluster-brennstoffzelle